Gigacasting: Revolutionising Automotive Manufacturing
We prototype large, single piece structural parts.
So cutting edge and top secret, we can barely talk about it.
"The masters of metal"
We're the world's leading independent gigacasting prototypers using sand casting.
Working with customers like:
Sorry,
but we
really can't
talk about them
What is gigacasting?
Why is it important?
What are the benefits?
What is Gigacasting?
Gigacasting is a cutting-edge manufacturing process that creates large, single-piece structural castings using high-pressure aluminium die-casting machines. Gigacasting is revolutionising the automotive industry, with projections indicating the gigacasting sector will grow from $751 million in 2023 to $2.6 billion by 2030, highlighting its transformative potential.
Many large OEMs have embraced gigacasting, representing a significant shift from traditional methods, typically the front and rear underbody structures. Many consider gigacasting essential for the success of the Electric Vehicle (EV) market as it can allow lighter vehicles that are better for the environment and cheaper to produce.
Before entering mass production with the costly high-pressure die-casting processes, these parts must be prototyped, which is where Grainger & Worrall's giga sand casting facility strives.
Multi material assembly
171
Parts
Gigacasting
0
Parts
>0
Fewer welds
How Does Gigacasting Work?
Gigacasting streamlines vehicle manufacturing by consolidating many smaller parts into one large structural component. For high volumes, this is done with high-pressure aluminium die-casting machines that inject molten metal into moulds. For prototyping or smaller volumes, sand casting can be used. Manufacturers typically use gigacastings for the front or rear under-body (FUB or RUB) of a vehicle's structure and have primarily been adopted in the automotive market, but could also be adopted by other markets in the future.
Gigacasting is often vertically integrated into OEM facilities, reducing the need for shipping and associated logistics, which can help lower the carbon footprint.
Why Is Gigacasting Important?
Gigacasting enables manufacturers to produce large, structural components in a single piece, simplifying assembly and reducing production complexity. It’s a sustainable manufacturing method, reducing material waste and helping to create greener, more efficient vehicles, especially in the EV market.
What are the Benefits of Gigacasting?
-
1. Fewer Parts, Greater Efficiency
Gigacasting eliminates the need for numerous smaller parts by producing large, structural components, such as an entire front underbody or even a full vehicle body, which streamlines production.
-
2. Better Stress Distribution
Single-cast parts have fewer weak points compared to traditional multi-part welded structures as stresses are more uniformly distributed.
-
3. Speeds Up Production
Gigacasting reduces assembly time and accelerates production cycles, helping manufacturers bring products to market faster.
-
4. Long-Term Cost Savings
While the initial investment in giga die-casting equipment is considerable, long-term savings and increased efficiency make it a valuable investment, reducing material waste and labour costs over time. Due to the high initial investment costs of giga die-casting machines, sand casting can be cheaply and effectively used to prototype the gigacastings. An invaluable stage in bridging the gap between concept and full-scale production.
-
5. Enhanced Flexibility
Gigacasting’s reduction in parts provides greater flexibility in design and manufacturing, improving supply chain efficiency.
-
6. New Solutions for Car Body Construction
Gigacasting solves engineering challenges like integrating new core parts, such as battery trays, especially for electric vehicles.
-
7. Precision and Accuracy
Gigacasting can deliver exceptional dimensional accuracy, surpassing traditional welded structures and ensuring superior component quality and uniformity.
What Challenges Does Gigacasting Bring?
Investment costs and space requirements are big things to consider with gigacasting. There can be a lot of money (and space) needed upfront to set up this new means of production and it may not always make financial sense.
Engineering challenges can also emerge with gigacasting. For example, it can be difficult for some engineers to achieve the wall thickness needed in the casting. In contrast, the traditional method of joining sheet metal pieces can be incredibly efficient and cost-effective with automation. Gigacastings can also be challenging to repair, often requiring the full replacement of the casting.
The role of sand casting in Gigacastings
Sand casting plays a huge role in prototyping gigacastings. Aluminium-silicon alloys can mirror the properties achieved in high-pressure die casting.
Prototyping with sand casting effectively produces precise, production-representative parts, with fast lead times. To validate part integrity and design, many automotive manufacturers have used sand casting to prototype components before moving to die-cast manufacturing. For manufacturers, this provides vital proof of concept during prototyping phases before investment in larger-scale production.
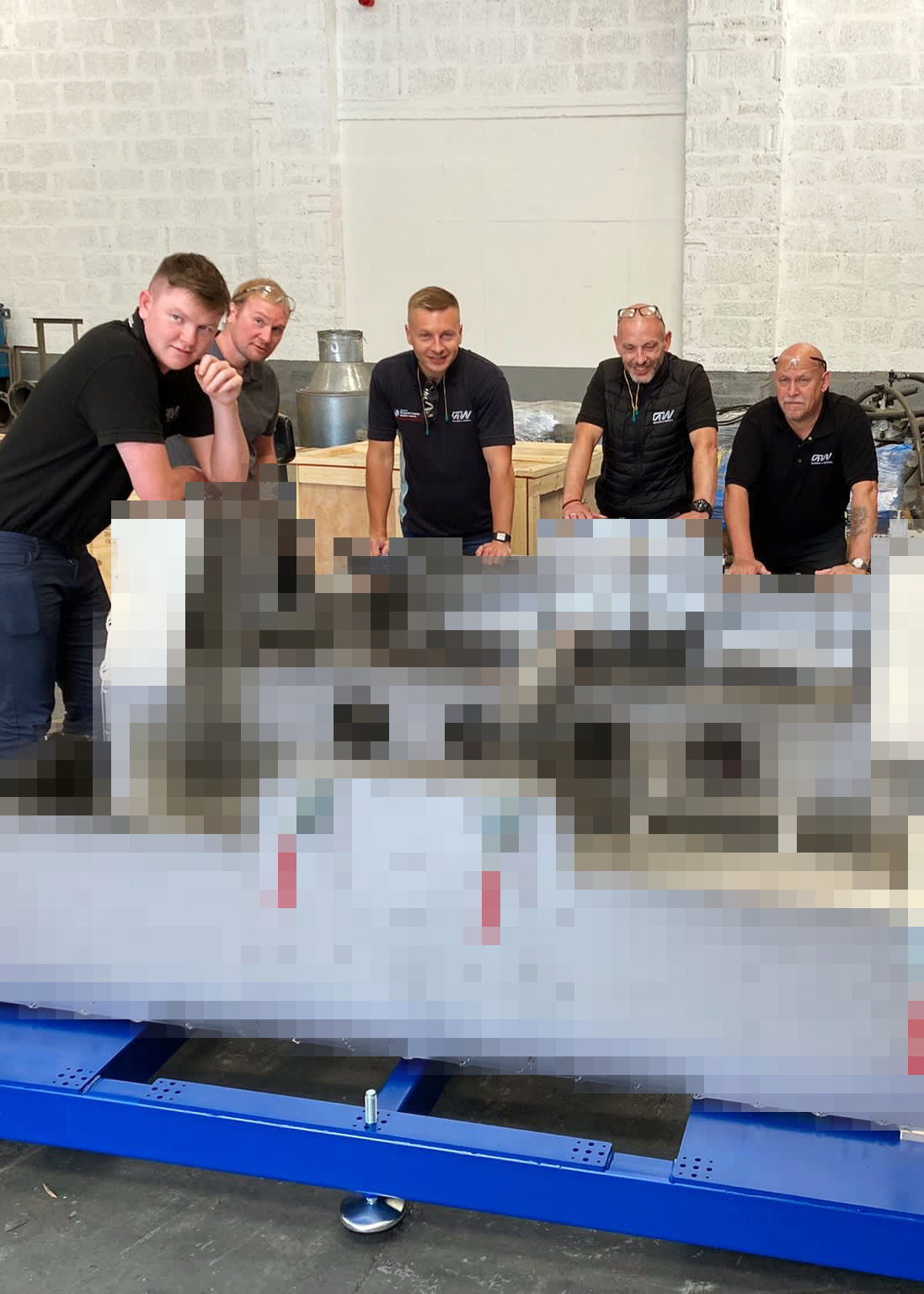
G&W: Expertise in Casting Large Structural Parts
Do you want to explore gigacasting for your business? Grainger & Worrall has extensive experience in casting technology for prismatic structures and has expanded its expertise to prototype large, structural body-in-white components with gigacasting.
This technology is becoming increasingly popular with customers who want to reduce component count and assembly time/costs by prototyping structural parts. We’ve also invested in a gigacasting facility for efficient, reliable and repeatable giga-cast prototypes.
Grainger & Worrall's innovative Giga Tile™ production method makes it possible to scale up the prototype process to a small low-volume series supply, thereby meeting the pre-production requirements of customers.
We’ve optimised our process to revolutionise the conventional sand-casting method, adopting 3D-printed core technology to facilitate rapid design changes if required.
Speak to our experts to find out more
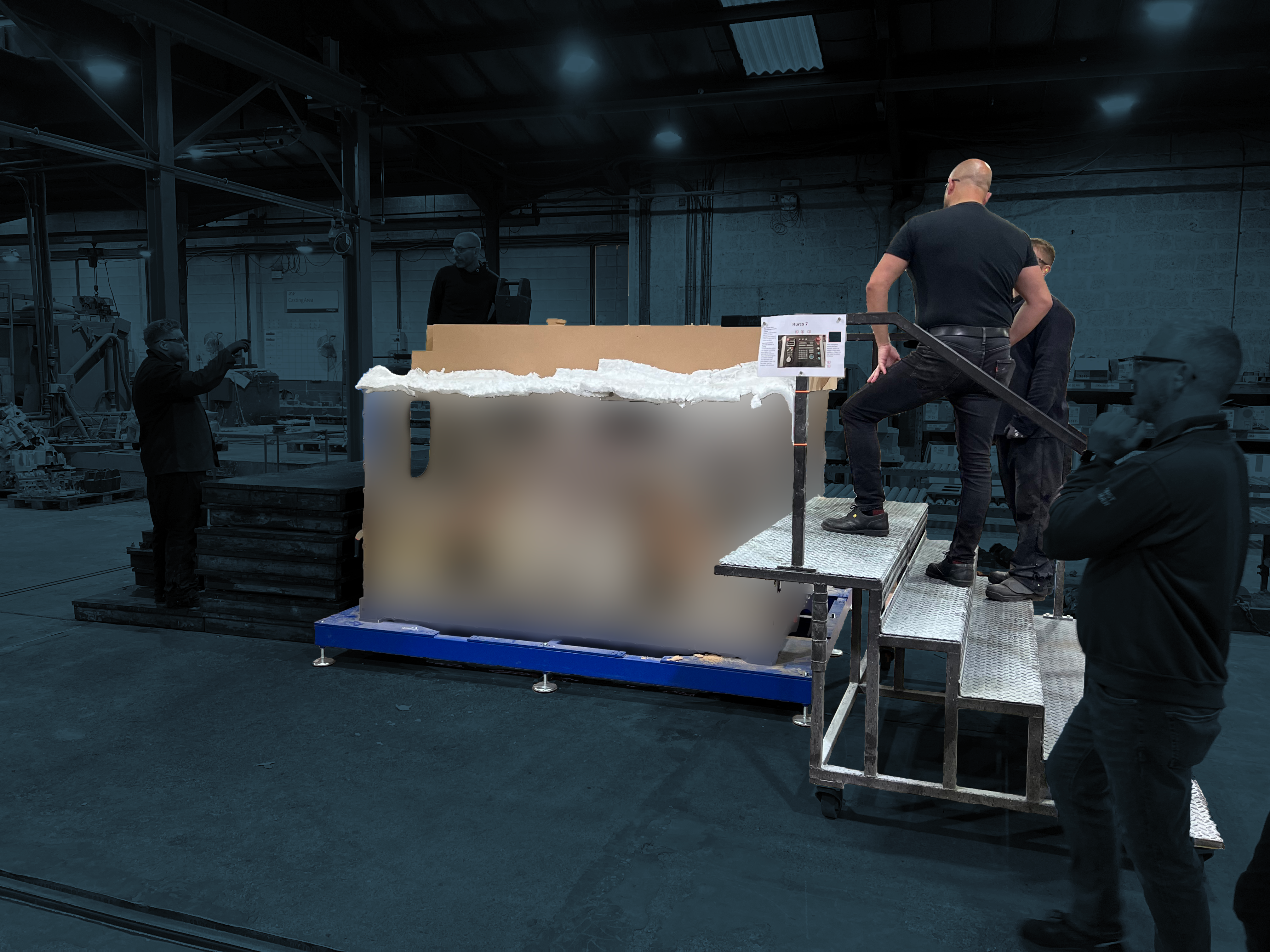
Driving a green agenda
Grainger and Worrall are committed to driving a sustainable operating model and continuing to develop our green agenda. We do this by focusing on the key areas of energy, environment, technology and lightweight.
